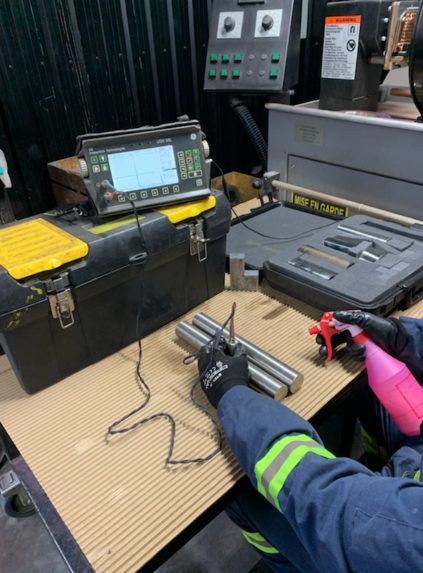
33
years
Experience
This involves the use of standard quality assurance practices and procedures throughout the various stages of manufacturing and processing, at ware-houses and materials receiving, and during fabrication and final installation of the product.
These guidelines are intended to aid employers in recognizing the essential factors to be considered in qualifying employees engaged in the major NDT methods.
Trained, Certified and knowledgeable inspector who have learned a skillset for fieldwork and a solid coatings foundation
In conventional ultrasonic examination inspection parameters are fixed and each inspection configuration has a fixed focal point and fixed incidence angle.
In a TOFD system, a pair of ultrasonic probes sits on opposite sides of a weld.
Corporate Level III – Represent your company as your Corporate Level III to assist in audits, documentation, training, procedures, and consultation.
Visual testing also known as visual inspection is one of the oldest and most common NDT technique which involves the operator looking at the test piece.
Non-Destructive Testing (NDT) is the process of testing of components or assembly for discontinuities without destroying the serviceability of the part or system.
Ultrasonics uses high Frequency sound waves in order to detect internal and external defects in welding, materials, and components.
Phased Array (PA) is an advanced technology becoming more and more available in the NDT industry to perform full weld inspections, stand alone or in lieu of Radiography.
Metal absorbs and then emits X-Rays. The emission spectrum is analyzed for characteristic (or fluorescent) X-Ray energy of the constituent elements.
Ferrite is a crystal structure type that gives iron its magnetic properties. The ferrite test establishes the predominance of this structure in a metal.
A small indentation is made in material. Comparing the size of this with a similar deformation in a known hardness standard yields a hardness value for the material under test.
Ultrasonics uses high Frequency sound waves in order to detect internal and external defects in welding, materials, and components.
Automated Ultrasonics (AUT) or Advanced Ultrasonics utilizes the same principles as conventional ultrasonics with the added benefit of a permanent record of inspection.
Liquid Penetrant Inspection method works by the application of a dye to the surface of a part. The dye will use a capillary action to penetrate into surface discontinuities.
By measuring the visible spectrum of a metal burning under an electric arc, this method can qualify the chemical makeup and grade of a metal under test.
The magnetic particles are drawn, and held to the surface of the part by the flux leakage which creates a visible indication of any discontinuities.
Corporate Level III – Represent your company as your Corporate Level III to assist in audits, documentation, training, procedures, and consultation.